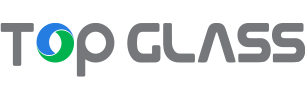
2020-01-14 16:42:24
Tapematic USA, Inc.: A Rich History of Innovation with a Personalized Touch
2020-01-14 16:42:24
Beauty Packaging: Innovation is at the heart of Tapematic’s business, beginning with your founder, Luciano Perego. What’s your mindset towards innovation?
Tony Denning: Nearly 50 years of experience has allowed Tapematic to build a huge resource of technical experience, as well as a more efficient and modern way of processing for the coating and metalllization of the objects. We study how objects are decorated and find areas to streamline/automate in an environmentally friendly way. We designed and developed our own paint booths from scratch and utilize HVLP (High Volume, Low Pressure) and Spray-on-Demand technology ensuring minimum coating waste. We also introduced Cold Cure UV curing, ensuring any IR heat from UV lamps is not directed toward the object being cured. In addition, we look to do more than just the coating and metallization by being able to add in-line quality inspection, auto loading and off-loading and in-line decoration. Tapematic listens to our customers and implements their ideas and desires into the line, making the line suited to their specific requirements.
BP: Tapematic is passionate about environmental stewardship. Tell us about your commitment to high-energy efficiency and waste/emissions minimization.
TD: Tapematic desires to produce the most environmentally friendly equipment for cosmetic part decoration. Being able to process 100% solid coatings is a huge step forward in this area, as this dramatically reduces the VOC output from the paint lines. Spray-On-Demand technology reduces waste of the paint. The line also consumes 40KW of electrical power; eight times less power consumption than traditional decorating lines. Plus, the factory is running near 100% on solar power.
BP: You recently celebrated your 50th PST line installation, as well as the launch of your PST II line. How does the PST II line position Tapematic to meet the needs of cosmetic/personal care customers?
TD: The PST II line offers more flexibility at a much higher output—nearly three times the output of a standard PST I line. Additionally, the part size that can be processed on a PST II line has increased to 102mm in diameter by 120mm in height, enabling our customers to process larger items such as glass bottles and larger closures for creams. The PST II line is also modular, allowing customers to expand the line as needed. The line can initially be configured as a coating line with a cleaning/pre-treatment module and a coating module, and metallization and topcoat modules can be added, with in-line decorating options.
BP: How does being an independent, family-owned business, help Tapematic meet the needs of beauty brands?
LinkedIn